海外低価格製品に対抗する驚異の戦略
日本のものづくりは新時代へ
武州工業株式会社 代表取締役 林英夫さん
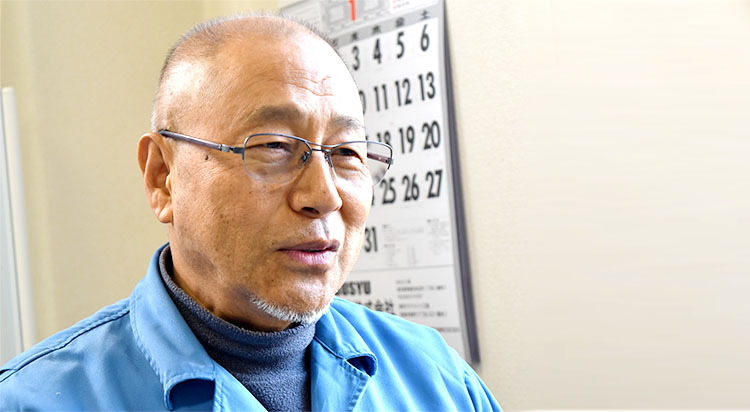
日本のものづくりは、海外の低価格製品との競争により苦境に立たされています。そんな中、希望の星と熱い注目を集めているのが、自動車用・医療用金属パイプの加工を行う武州工業株式会社です。多くの製造業が生産拠点を海外にシフトさせる中、同社は自社製の設備や独自の生産システムを導入し、徹底的にコストを削減することで、海外の低価格製品への対抗に成功しました。同社が低価格を達成できるのは、海外の安い人件費に習って、人件費を削減しているからではありません。同社の製品はどのようにして生まれるのか、また、ものづくりにこめた思いとはどういうものか――。日本のものづくりの最先端を走る、同社代表取締役の林英夫さんにお話をうかがいました。
(聞き手:株式会社natural rights代表取締役 小酒部さやか)
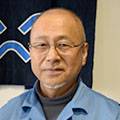
- 林 英夫さん
- 武州工業株式会社 代表取締役
はやし・ひでお/1952年、東京都青梅市に生まれる。1974年日本大学生産工学部電気工学科電気・電子専攻卒業。1992年武州工業株式会社代表取締役就任。2012年ITコーディネータ協会つなぐIT推進委員就任。2017年「日本で一番大切にしたい会社大賞」審査委員会特別賞受賞
三つの取組みにより実現した高い競争力
海外に生産拠点を持たない貴社が、海外の低価格製品に対抗できる製品を作り出すことができるのはなぜでしょうか。
海外の製品が安いのは、人件費が低いからです。日本では海外の水準まで人件費を下げることはできないので、徹底したコスト管理で対抗するしかありません。また、品質や納期などで強みを出すことも重要です。
そのために、次の三つのことを実践しています。
(1)自社設備を開発する
(2)1個流し生産方式をとる
(3)情報管理システムを徹底的に活用する
これらがうまく組み合わさり機能していることが、当社独自の強みと言えます。
三つの取り組みの中からまず、「自社設備を開発する」ことのメリットを教えてください。
自社設備の開発といっても、オーダーメイドの機械を外注しているわけではありません。当社には開発部があり、作業内容に特化した機械を開発します。ちなみに開発部には、現場スタッフの中から選ばれた20人が配属されています。
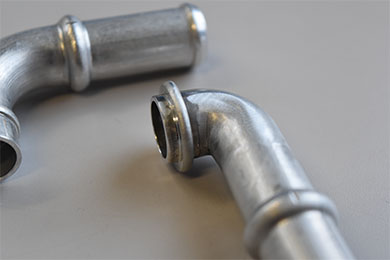
自社内で設備を開発すると、大幅にコストダウンできます。例えば購入すると4000万円かかる機械が、1000万円くらいで製作できる。また、既製品は機能が豊富で最大出力も高く設定されているために筐体が大きく、広いスペースが必要ですが、自社内で開発すると必要最小限の機能と出力に合わせられるので、電力もスペースも節約できます。当然、作業効率は上がり、時間の節約にもなります。また、自社内での開発により、「1個流し生産方式」が真価を発揮できています。
ライン生産よりも高い生産力
「1個流し生産方式」とはどういうものですか。
「1個流し」とは、一人で多くの工程を受け持ち、材料を最初から最後まで加工する方法です。ここで自社開発したミニ設備が活躍します。作業スペースに無駄がなくなり、最小限の動きで最後まで加工できるようになるからです。
ラーメン屋の調理場をイメージしていただければわかりやすいと思います。カップ麺などの量産ラインとは異なり、店頭では個別の注文に柔軟に応じながら早く提供することができます。また仕掛品をかかえ込まなくてすむため、在庫コストやリスクを減らせます。
ポイントは、時間の使い方です。加工の中には、長く時間が必要になる工程があります。ライン生産では直列に時間が足されていきますが、1個流し生産では、それ以外の工程を並列して終わらせるようにしています。それによって、ライン生産以上の生産力を持てるようになります。
また、1個流しでは、工程の中に品質検査も組み込んでいます。不具合品が出ると先に進めないようにシステムを作り、品質検査の手間を大幅に削減することができました。また、工程内で不具合品が明確になるので、全製品を回収するなどのリスクはほぼゼロになります。
「情報管理システムの活用」についてお聞かせください。
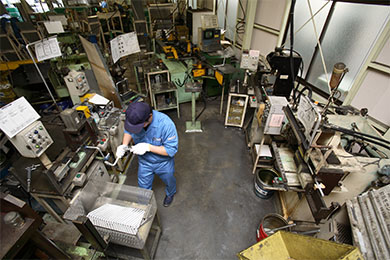
当社は自社内で、BIMMSと呼んでいる情報管理のプログラムを作りました。スタッフは出社時にこのプログラムに各自の体調を入力することで、ログインできます。仕事でもこのBIMMSに入力しなければ作業が進められないように組み込まれています。
このプログラムは基本的に、あらゆる情報を「見える化」するためのもので、大きく分けて三つのメリットがあります。一つ目は、リアルタイムな在庫管理によって無駄な製品を減らせること。BIMMSによって、素材在庫と製品数がリアルタイムでわかるようにしています。コンビニの発注システムを想像されるとわかりやすいでしょう。注文状況と在庫がわかるようになっているので、製作の優先度がわかりますし、予測を立てて備えることもできます。その結果、必要な時に必要なだけ製品を作ることができるようになりました。
二つ目は、社員が不正をしなくてもいい環境を作れること。BIMMSを使えば、消費した素材とできた製品の突き合わせが簡単に行われるので、不具合品数などのごまかしができないようになっています。また、当社では品質検査を、朝、昼、夕と、3回に分けて行なっているのですが、紙に報告を書いていると、本当にその時間にチェックしたのかどうかがわかりません。そこで、BIMMSでチェック項目を入力するようにし、全て時間の履歴が残るようにしました。作業全般にわたって、このような不正やごまかしをしても意味がない環境を作ることができ、大きなトラブルを防ぐことができています。
三つめは、社員教育のために情報を活用できること。BIMMSを使って生産に必要な情報を見える化することで、知識や技量の格差をなくしています。その他にも、当社は「見え太」くんというアプリを作り、スマートフォンなどの万歩計機能や位置センサーを利用して、作業ペースを見える化しました。時間帯による作業集中度の濃淡や不具合品の割合、製品ごとの生産力といったデータがリアルタイムでBIMMSに送信され、わかりやすく集計されます。これによって、個人が自分の「クセ」を把握しやすくなり、生産力の向上につながっています。
これらが総合的に組み合わされることで、最適な作業環境と高い生産力、適正な在庫管理とリスク管理を達成することができ、製品のコストダウンに成功し、海外製品にも対抗できるようになっています。
地域の雇用を守る それが全て
複数の作業を行う1個流しなど、貴社の社員には習熟した技術を持つことが求められそうですね。他に教育方法で工夫されていることがあれば教えてください。
当社では、入社時の研修で、最高難易度と言われる「アルミのろう付け」を習得してもらいます。アルミは鉄と違って、バーナーで熱しても色が変わりません。温度変化を見極めるのが難しい上に、ろう付けに最適な温度は、770度から800度の、わずか30度の間です。それ以上熱すると母材が溶けてしまうので、一瞬の油断もできません。
かつては名人の技とされ、技術を持つ人は本当に限られていました。当社では2週間でこれを習得してもらいます。すると、難易度の低い技術も同時に学べます。本人には自信がつきますし、最高難易度の技術を全員が持つことによって技術や仕事を属人化せずに、ノウハウを普及しやすい環境になっています。
緻密に作り上げられた経営システム・製作環境ですが、このシステムを作り上げた背景をお聞かせください。
結局のところ、日本のものづくりを守りたい、地元の雇用を守りたい、という気持ちに尽きると思います。いかに海外製品に対抗するのか、その一点をこれまで真剣に考えてきました。
当社は雇用を守るため、会社の財務状況を社員に公開し、利益を社員に分配しています。また、採用するのは、会社所在地である青梅近隣の人材がほとんどです。勤務時間は8時から17時までで、残業をなくすために努力しています。交代制は採用していません。1ヵ月の稼働日は20日間で、自分の時間を大切にしてもらっています。スタッフは全員正社員で、リストラもありませんし、離職率も低い。地域の雇用を守りたいという気持ちが伝わるからこそ、社員は会社のために頑張ってくれるのだと思います。なんのために仕事をするのか。それが全てではないでしょうか。
本日は、貴重なお話をありがとうございました。
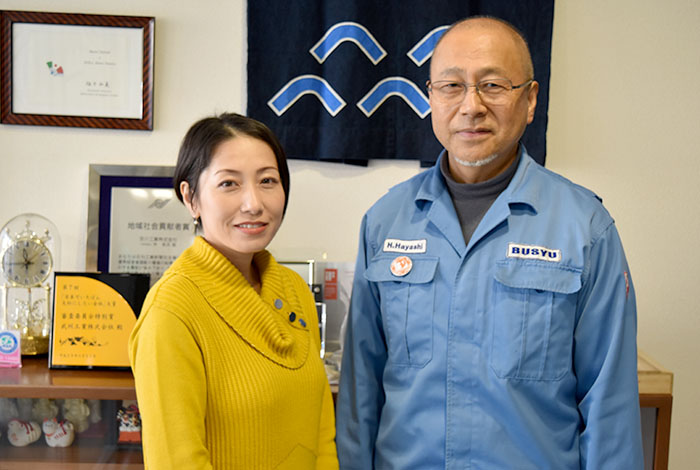
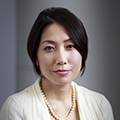
取材:小酒部さやか(株式会社natural rights 代表取締役)
2014年7月自身の経験からマタハラ問題に取り組むためNPO法人マタハラNetを設立し、マタハラ防止の義務化を牽引。2015年3月女性の地位向上への貢献をたたえるアメリカ国務省「国際勇気ある女性賞」を日本人で初受賞し、ミシェル・オバマ大統領夫人と対談。2015年6月「ACCJウィメン・イン・ビジネス・サミット」にて安倍首相・ケネディ大使とともに登壇。2016年1月筑摩書房より『マタハラ問題』、11月花伝社より『ずっと働ける会社~マタハラなんて起きない先進企業はここがちがう!~』を出版。現在、株式会社natural rights代表取締役。仕事と生活の両立がnatural rights(自然な権利)となるよう講演・企業研修などの活動を行っており、Yahooニュースにも情報を配信している。
ライター:水野宏信- 参考になった0
- 共感できる0
- 実践したい0
- 考えさせられる0
- 理解しやすい0
無料会員登録
記事のオススメには『日本の人事部』への会員登録が必要です。